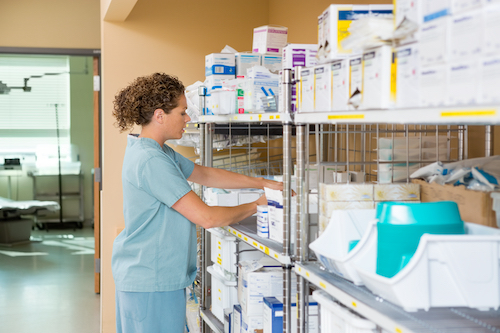
There’s no getting around it. Inflation has permeated every aspect of the economy – including the healthcare supply chain. Raw materials, energy, labor and logistics have all been affected, said Margaret Steele, Vizient Senior Vice President, Med/Surg.
Indeed, over the 12 months from February 2021 to February 2022, the Consumer Price Index, which measures the average prices of consumer goods and services, increased 7.9% to a four-decade high.
Labor costs rose 4% to 8% with manufacturers and freight companies struggling to attract workers and drivers. In the healthcare sector, escalating labor costs have been particularly painful. In its February National Hospital Flash Report, Kaufman Hall found that from December to January labor expense per adjusted discharge climbed 14.6%.
Through the last year and a half (since fall 2020) energy, resins, cotton and most metals have all surged in excess of 30%. “With the recent upturn of oil prices, the rate of inflation will continue this upward trend,” Steele said. “These levels of inflation are impacting manufacturers and service providers significantly and they have begun raising prices on the supplies, equipment, and services they deliver to hospitals.”
Global events hit home
Steele said the healthcare supply chain has been significantly impacted over the last several years due to many factors including world events. As a result, timely and accurate information is critical to minimize impact and determine risk mitigation strategies.
“Supply chain leaders use various tools, such as budget impact projection reports, market supply updates and category specific insights, to understand the impact of changes affecting raw materials, labor and logistics as they look to understand cost and risk for supply disruption,” Steele said. Now, supply chain leaders are utilizing these same sources to monitor the impact of the recent events that also have an impact on raw materials, manufacturing and transportation.
Steele projects the most impactful and of most interest will likely be oil as so many products contain some form of plastic or resin (a derivative of oil). In mid-March, resin prices remained higher than pre-COVID levels and were expected to remain so as long as oil remains near or above $80 per barrel and producers continue struggling to get resins moved through the supply chain. Both issues are anticipated to remain through most of 2023. Oil price fluctuation, trucker shortages and port backups will also impact the costs for transporting products to the provider locations.
“Many products have not yet been impacted as the situation is affecting raw materials,” Steele said. “That said, impact mitigation strategies vary by location and provider type. Providers are sharing conservation strategies in efforts to reduce usage as appropriate, pre-qualifying alternative products in the event of a disruption, increasing product on hand (or at a distributor/partner location) and ensuring product is sourced from a variety of locations. Several suppliers have medical teams that will work with the providers directly to discuss alternative uses. And, many are also participating in commitment programs, wherein suppliers and providers agree on a longer, committed supply and in some cases pricing.”
While GPO and self-negotiated contracts are keeping prices fairly stable at the moment, supply chain leaders fully expect to see significant price increases in the next series of contracts, said Mike Schiller, senior director of supply chain at the Association for Health Care Resource & Materials Management (AHRMM) of the American Hospital Association (AHA).
“Many are anticipating high single to low double digit price increases and have begun to include these into their budgetary considerations.”
Filed Under: Repertoire’s Dail-eNews